Modern Modalities of the GTAW Process to Increase Productivity
- Rafael Nunes
- Apr 8, 2020
- 3 min read
Updated: May 13, 2020
Do you know the new modalities of the GTAW process?
In the manufacture of pipelines, the first welding step, known as the root pass, is considered a critical step in the execution of the joining, due to its structural importance of support for the subsequent passes. Commonly, the root pass is performed by the GTAW (Gas Tungsten Arc Welding) process, also known as TIG (Tungsten Arc Welding), and then the chamfer is filled by the SMAW (Shielded Metal Arc Welding) or GMAW (Gas Metal Arc Welding), manually or automatically, causing difficulty in achieving the required quality.

The GTAW process allows for better metallurgical quality when compared to other traditional welding processes, such as the GMAW process. However, this process presents a great disadvantage when analyzed by its deposition rate and the consequent productivity of the process. Also, when executed manually, it requires greater experience and practical knowledge of the operator. The process, by allowing an independence in the rate of material fed with the heat supplied to the workpiece, allows a wide control of the aspects that contribute to a welding with high metallurgical quality, such as control of penetration, wettability, dilution, etc.
Due to the presence of a non-consumable electrode close to the molten filler material, there is a high tendency and possibility of contamination of this electrode. This is especially critical in orbital welding procedures, where welding out of position is more complex and susceptible to the appearance of defects and contamination of the electrode, due to the action of the gravitational force in the opposite direction to the melting pool.
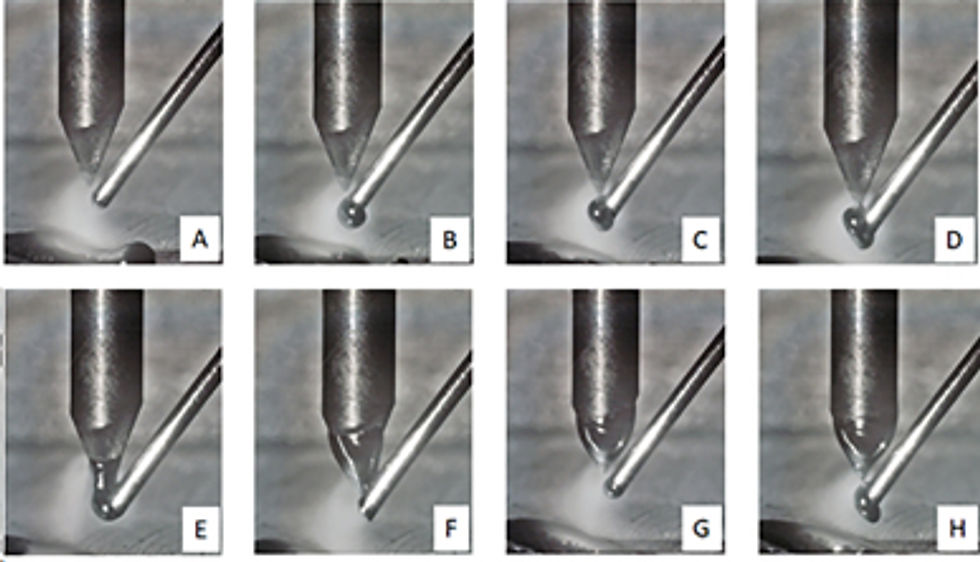
In this scenario, with the aim of increasing productivity, quality and robustness of the GTAW process. Among these, one can mention:
GTAW Hot Wire

The preheating of the wire is generated by a second current, of less intensity, transmitted by the filler material. This current favors its heating by Joule effect, making it even pre-heated. Thus, the filler material needs less energy to be melted, so a higher deposition rate can be used when compared to the conventional process. The GTAW Hot Wire process is also used in coating processes, where preheating assists in the execution of coating with reduced dilution values. Understand the importance and influence of dilution on the cladding processes in our article.
GTAW With Dynamic Wire Feeding

Dynamic wire feed can be used in low and high frequency. Both techniques favor several benefits to the conventional process. Regarding the robustness of the process, it is known that dynamic wire feeding helps in the process’s robustness, making the metallic transfer of the filler material more uniform and constant, while also sustaining several metallurgical benefits, such as lower dilution, less porosity formation, increased solubility of precipitates, among others.
GTAW With Tangential Wire Feeding

The electric arc of the GTAW process is formed by several isotherms in decreasing order of temperature from internal to external isotherms. When using tangential wire feeding, the filler material is fed and directed by the isotherms closest to the center of the arc, i.e., the isotherms with the highest temperature. Thus, suffering greater influence from the heat generated by the arc, it is possible to use higher wire feed rates when compared to the conventional process. Still, some authors indicate that this modality of the GTAW process allows it to be used in any wire feed direction without affecting the quality of the process, in a way opposite to that observed in the conventional GTAW process.
GTAW Double Electrode
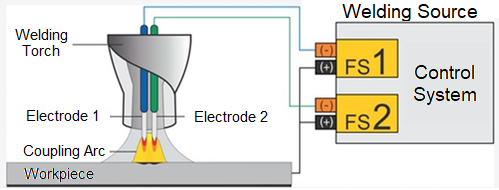
GTAW double electrode process, also known as multi-cathode GTAW and GTAW Twin, employs two tungsten electrodes in thCe same welding torch in independent electrical systems, each with its respective power source. The welding is then carried out by means of a single arc (coupling arc), composed by the interaction of the arcs generated in the two electrodes by the welding sources. The arc resulting from the coupling has less pressure, a fact that reduces the occurrence of discontinuities in the weld bead and allows for increases in the welding current and speed.
Each of these mentioned aspects will be discussed in detail in the next articles. Stay on top of all the news and curiosities in the world of welding through The Welding Land.
References: Silva RGN., Caracterização do Processo de Soldagem TIG com Alimentação de Arame Dinâmica em Alta Frequência, Trabalho de Conclusão de Curso, Engenharia de Materiais, Departamento de Engenharia Mecânica, Universidade Federal de Santa Catarina, 2017 Silva RGN, Estágio Obrigatório de Estágio II, Engenharia de Materiais, Departamento de Engenharia Mecânica, Universidade Federal de Santa Catarina, 2013 Silva RHG, Silva RGN, Schwedersky MB, Dalpiaz G, Dutra JC. Contributions of the high frequency dynamic wire feeding in the GTAW process for increased robustness. Soldagem & Inspeção. 2019;24:e2430. https://doi.org/10.1590/0104-9224/SI24.30 Godinho C, Avaliação Experimental do Processo de Soldagem TIG Automatizado Alimentado com Reduzidos Ângulos de Inserção de Arame em Relação ao Eletrodo, Trabalho de Conclusão de Curso, Engenharia de Materiais, Departamento de Engenharia Mecânica, Universidade Federal de Santa Catarina, 2017
Kommentare